Polypropylene fibre
Some advantages of pp fiber
Compressive Strength: Micro silica enhances the compressive strength of concrete. It reacts with the calcium hydroxide in the cement paste to form additional calcium silicate hydrate (C-S-H), which contributes to a denser and stronger matrix.
Flexural Strength: It also improves the flexural strength of concrete, making it more resistant to bending forces.
Reduced Permeability: The use of micro silica reduces the permeability of concrete, making it less susceptible to water ingress and chemical attack. This enhances the longevity of structures.
Resistance to Chemical Attack: Concrete containing micro silica has better resistance to aggressive environments, such as exposure to sulfates and chlorides.
Smoother Finish: Micro silica can improve the workability and smoothness of the concrete mix, making it easier to handle and finish. This can lead to a better surface appearance and reduced finishing time.
Shrinkage Reduction: By enhancing the density of the concrete matrix, micro silica helps to reduce shrinkage, which can lead to fewer cracks during the curing process.
Crack Resistance: The improved microstructure of the concrete helps in controlling and minimizing cracks, which contributes to the structural integrity and aesthetics of the finished product.
how to use / uses
Determine Requirements: Assess the specific needs of your project, including structural requirements, environmental conditions, and desired concrete properties.
Consult Professionals: Work with structural engineers or concrete specialists to determine the appropriate amount of micro silica and mix design based on your project's requirements.
Type: Choose a high-quality micro silica that meets industry standards. Micro silica is available in various grades, so select one that is suitable for your concrete mix.
Dosage: The typical dosage ranges from 5% to 10% by weight of cement. The exact amount depends on the desired concrete properties and mix design.
Adjust Mix Proportions: Incorporate micro silica into the concrete mix design. You may need to adjust the proportions of other mix components (e.g., cement, aggregates, water) to maintain the desired workability and strength.
Trial Mixes: Conduct trial mixes to determine the optimal dosage and mix proportions. Test the trial mixes for workability, strength, and other properties to ensure they meet project specifications.
Batching: Accurately measure and batch all components of the concrete mix, including micro silica. Micro silica is usually added as a dry powder.
Dry Mixing: Add micro silica to the dry mix of cement and aggregates before adding water. This helps in achieving a uniform distribution of the micro silica particles.
Mixing: Use a concrete mixer suitable for handling micro silica. Ensure that the mixing time is sufficient to achieve thorough dispersion and integration of the micro silica into the mix.
Placement Techniques: Pour and place the concrete using standard methods. Ensure that the placement process does not cause segregation or clumping of the micro silica.
Compaction: Use proper compaction techniques, such as vibration, to remove air bubbles and ensure that the concrete mix is well-compacted and evenly distributed.
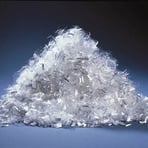
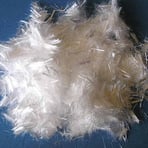
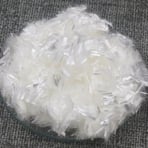
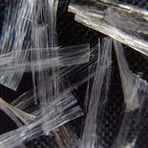
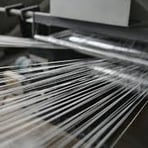
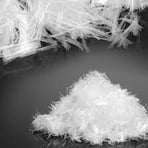
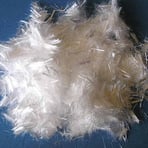
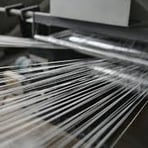